Occasionally we find a Continental W670, Lycoming R680, or Jacobs R755 engine that in running higher than normal oil temperatures. Often these engines are low time since the most recent overhaul, so the high oil temps are unexpected. I would like to address this with a few things that we have discovered.
Several years ago we were shipped a freshly overhauled W670 that was experiencing high oil temperature problems. Oil pressure was perfect, but after 30 minutes the temperature went to redline. We tried a few external things to no avail before starting to tear it down. The engine was mostly disassembled when one of our mechanics noticed that an 1/8” pipe plug was missing on the inside of the power case (arrow in the photo).
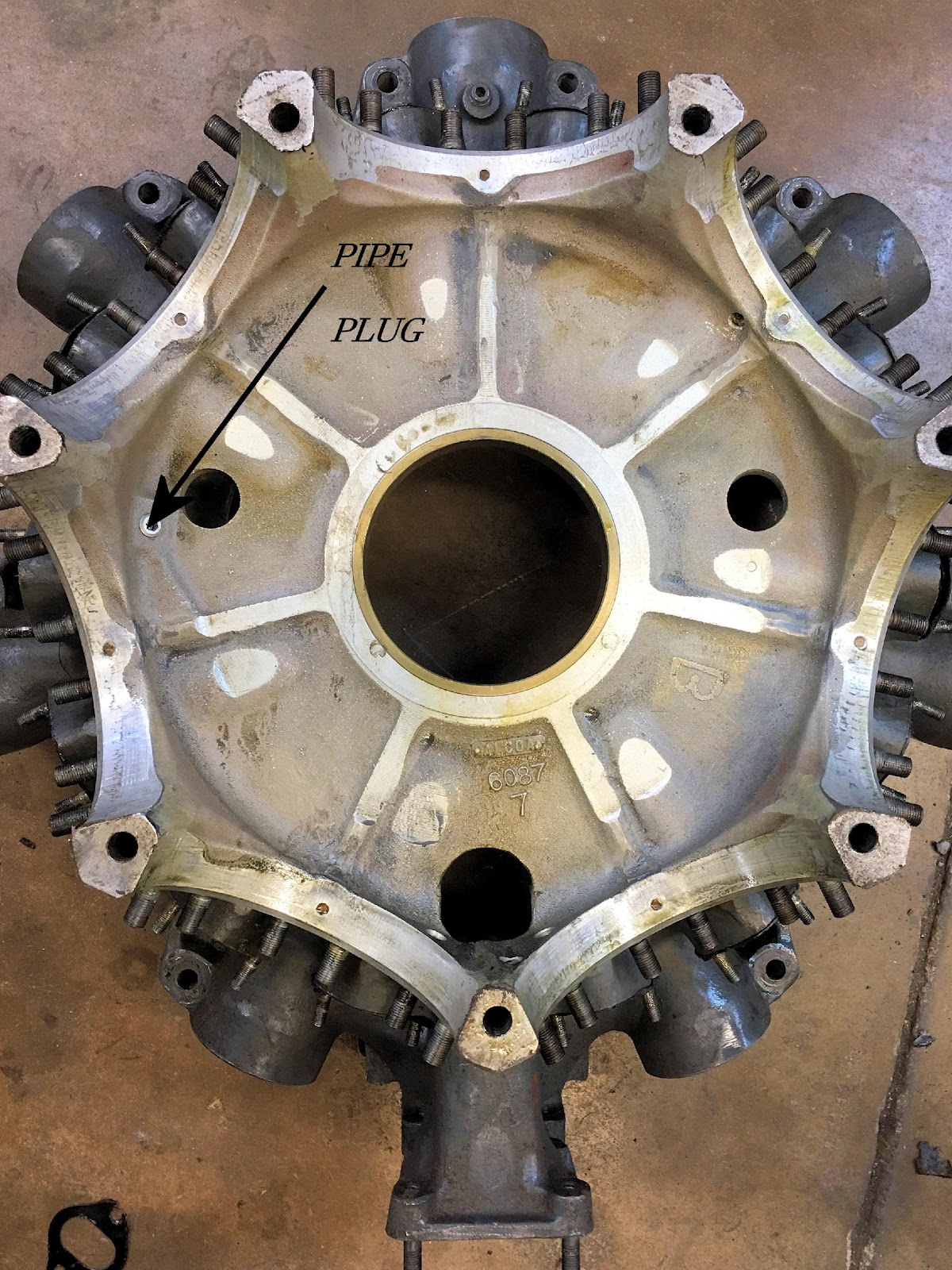
That oil passage is in the low-pressure side (rocker arm oiling) of the system. Apparently missing that plug in that location was not enough to affect the oil pressure, but it surely did heat things up. Since then we have seen five or six instances of the same problem—it is an easy thing for overhaulers to miss. After scratching our heads on that first one it is rather fun now when someone calls with a newly overhauled engine that has good oil pressure but is heating up. The fix is fairly simple: Pull the #3 cylinder, install the missing plug, and voila, all is better.
Another situation that creates similar symptoms to those mentioned above is found when a W670 crankshaft is installed which has been drilled for cold weather operation. On some of the Continental engines that were originally destined for Canada, a #58 hole was drilled in the rear crankshaft half expansion plug. This is a high-pressure location and it is truly amazing how much hot oil you can get through a .042” hole at 75 psi. The symptoms, though, were the same: good oil pressure and high oil temperature. A few years ago Pete Jones and I discussed all this at length before both of us decided to plug all those holes. Since then high oil temps in freshly overhauled W670 Continentals have not been an issue.
In the Pre-War Jacobs R755 engines the master rod bearing to crankpin diametrical clearance was .0025” to .004” with an end clearance of .010”, which was in keeping with the master rod bearing clearances of the other small radial engines of that era. Along came WWII and a military requirement for the manufacturers of engines used in training aircraft that they do whatever they deemed necessary to the design of their engines so the oil would not need to be changed between overhauls (!). See Lycoming Service Letter #110 dated 11/10/44. Different manufacturers made different changes. Some opened up oil jets, some machined flats on oiling holes (both in an attempt to avoid sludge build up). Jacobs opened up their master rod bearing to crankpin clearance to .004”-.0055” with a service limit of .008”. The new master rod end clearance went to .018”-.023”, replace at .040”. Just a few thousandths of an inch, right? But the engine oil temperatures now went up. Prior to WWII many of the Jacobs installations did not have oil coolers at all. Now they were a must. The Cessna 195 went from one, to two, to an almost unbelievable three on a few of them (and the third one had an electric fan!).
In the early 80s we hired an engineer to tackle the Jacobs hot oil problem. He ran the calculations sent me his analysis of the oil flow through the master rod bearing at various clearances. It turns out that increasing the diametrical or end clearance by only one or two thousandths increased the oil flow through the bearing by a factor of ten. That oil was spraying on the cylinders and picking up excessive heat. Based on that data we built a Jacobs engine using the pre-war dimensions, and the oil temperature problem went away. In 1989 we obtained FAA approval to again use the pre-war clearances and have had much better success keeping the oil temps down.
The common thread in all three of these stories seems to be this: an excess of oil spraying around on the hot cylinder bases picks up a lot of heat. Both the Continental and Jacobs oil pumps are capable of producing enough volume and pressure to keep up with any number of internal leaks. However, inside the engine more oil = more heat, and our engines are designed to be primarily air-cooled and not oil-cooled.
Occasionally we find a Continental W670, Lycoming R680, or Jacobs R755 engine that in running higher than normal oil temperatures. Often these engines are low time since the most recent overhaul, so the high oil temps are unexpected. I would like to address this with a few things that we have discovered.
Several years ago we were shipped a freshly overhauled W670 that was experiencing high oil temperature problems. Oil pressure was perfect, but after 30 minutes the temperature went to redline. We tried a few external things to no avail before starting to tear it down. The engine was mostly disassembled when one of our mechanics noticed that an 1/8” pipe plug was missing on the inside of the power case (arrow in the photo).
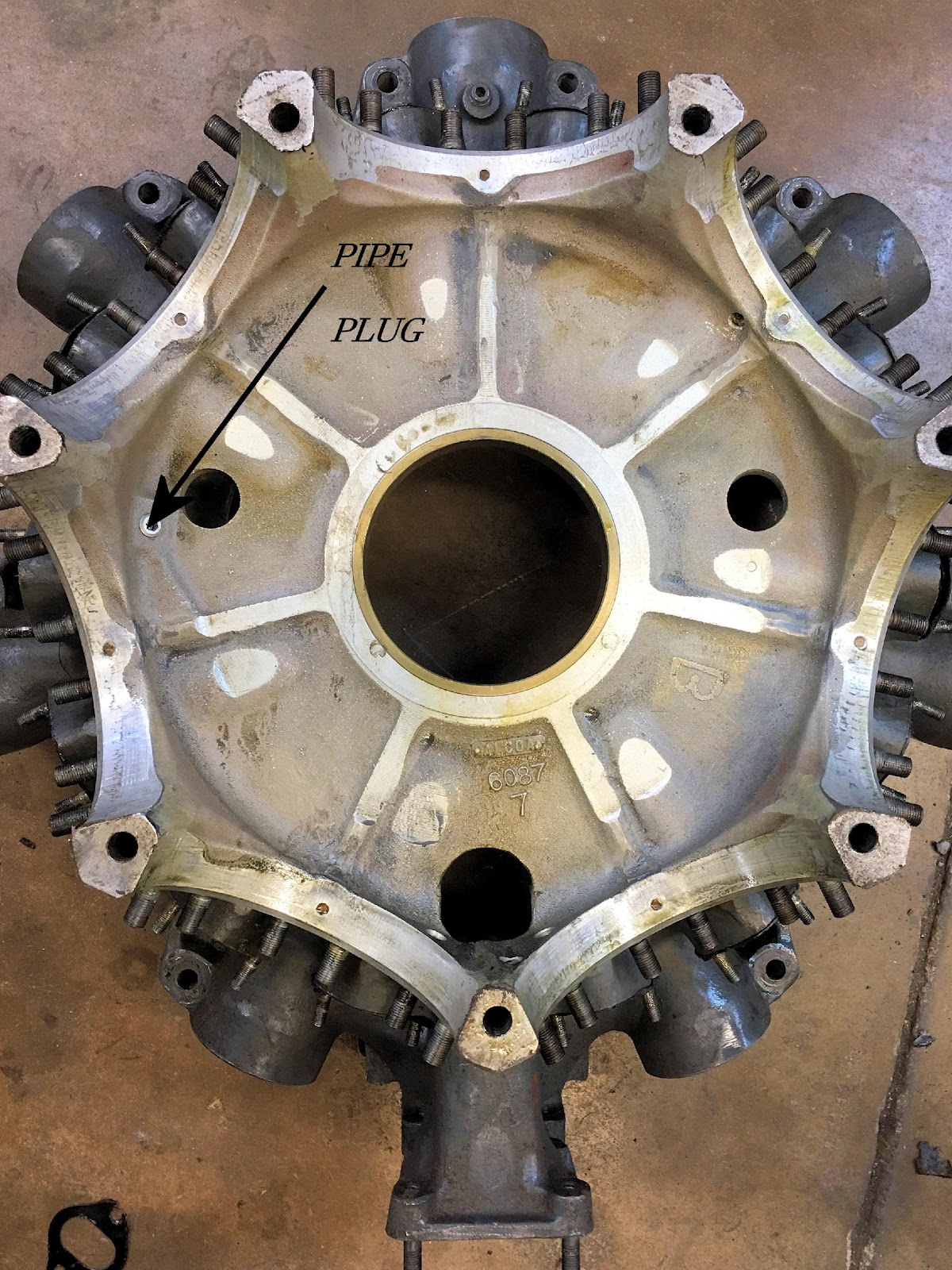
That oil passage is in the low-pressure side (rocker arm oiling) of the system. Apparently missing that plug in that location was not enough to affect the oil pressure, but it surely did heat things up. Since then we have seen five or six instances of the same problem—it is an easy thing for overhaulers to miss. After scratching our heads on that first one it is rather fun now when someone calls with a newly overhauled engine that has good oil pressure but is heating up. The fix is fairly simple: Pull the #3 cylinder, install the missing plug, and voila, all is better.
Another situation that creates similar symptoms to those mentioned above is found when a W670 crankshaft is installed which has been drilled for cold weather operation. On some of the Continental engines that were originally destined for Canada, a #58 hole was drilled in the rear crankshaft half expansion plug. This is a high-pressure location and it is truly amazing how much hot oil you can get through a .042” hole at 75 psi. The symptoms, though, were the same: good oil pressure and high oil temperature. A few years ago Pete Jones and I discussed all this at length before both of us decided to plug all those holes. Since then high oil temps in freshly overhauled W670 Continentals have not been an issue.
In the Pre-War Jacobs R755 engines the master rod bearing to crankpin diametrical clearance was .0025” to .004” with an end clearance of .010”, which was in keeping with the master rod bearing clearances of the other small radial engines of that era. Along came WWII and a military requirement for the manufacturers of engines used in training aircraft that they do whatever they deemed necessary to the design of their engines so the oil would not need to be changed between overhauls (!). See Lycoming Service Letter #110 dated 11/10/44. Different manufacturers made different changes. Some opened up oil jets, some machined flats on oiling holes (both in an attempt to avoid sludge build up). Jacobs opened up their master rod bearing to crankpin clearance to .004”-.0055” with a service limit of .008”. The new master rod end clearance went to .018”-.023”, replace at .040”. Just a few thousandths of an inch, right? But the engine oil temperatures now went up. Prior to WWII many of the Jacobs installations did not have oil coolers at all. Now they were a must. The Cessna 195 went from one, to two, to an almost unbelievable three on a few of them (and the third one had an electric fan!).
In the early 80s we hired an engineer to tackle the Jacobs hot oil problem. He ran the calculations sent me his analysis of the oil flow through the master rod bearing at various clearances. It turns out that increasing the diametrical or end clearance by only one or two thousandths increased the oil flow through the bearing by a factor of ten. That oil was spraying on the cylinders and picking up excessive heat. Based on that data we built a Jacobs engine using the pre-war dimensions, and the oil temperature problem went away. In 1989 we obtained FAA approval to again use the pre-war clearances and have had much better success keeping the oil temps down.
The common thread in all three of these stories seems to be this: an excess of oil spraying around on the hot cylinder bases picks up a lot of heat. Both the Continental and Jacobs oil pumps are capable of producing enough volume and pressure to keep up with any number of internal leaks. However, inside the engine more oil = more heat, and our engines are designed to be primarily air-cooled and not oil-cooled.